Risky Business - 5 steps to Risk Assessment
5 Steps to Risk Assessment
As an employer you have a duty of care to assess the health and safety risks faced by your workers. Accident prevention goes hand in hand with risk minimisation and neither is possible without a thorough assessment of what the risks are. You must systematically check for possible physical, mental, chemical and biological hazards.
There is no "one size fits all" risk assessment. Every business needs a risk assessment but each will be different as every business and premises will pose different risks. A risk assessment provides employers with the evidence you need to demonstrate how far you have gone to make a situation as safe as possible. Remember that you aren't expected to eliminate all risks. But you make sure you know about all the main risks and the things you needs to do to manage them responsibly. At ETD Training we are committed to ensuring that businesses are compliant with health and safety laws. Our courses are written by industry experts and our training and advice is aligned with HSE thinking.
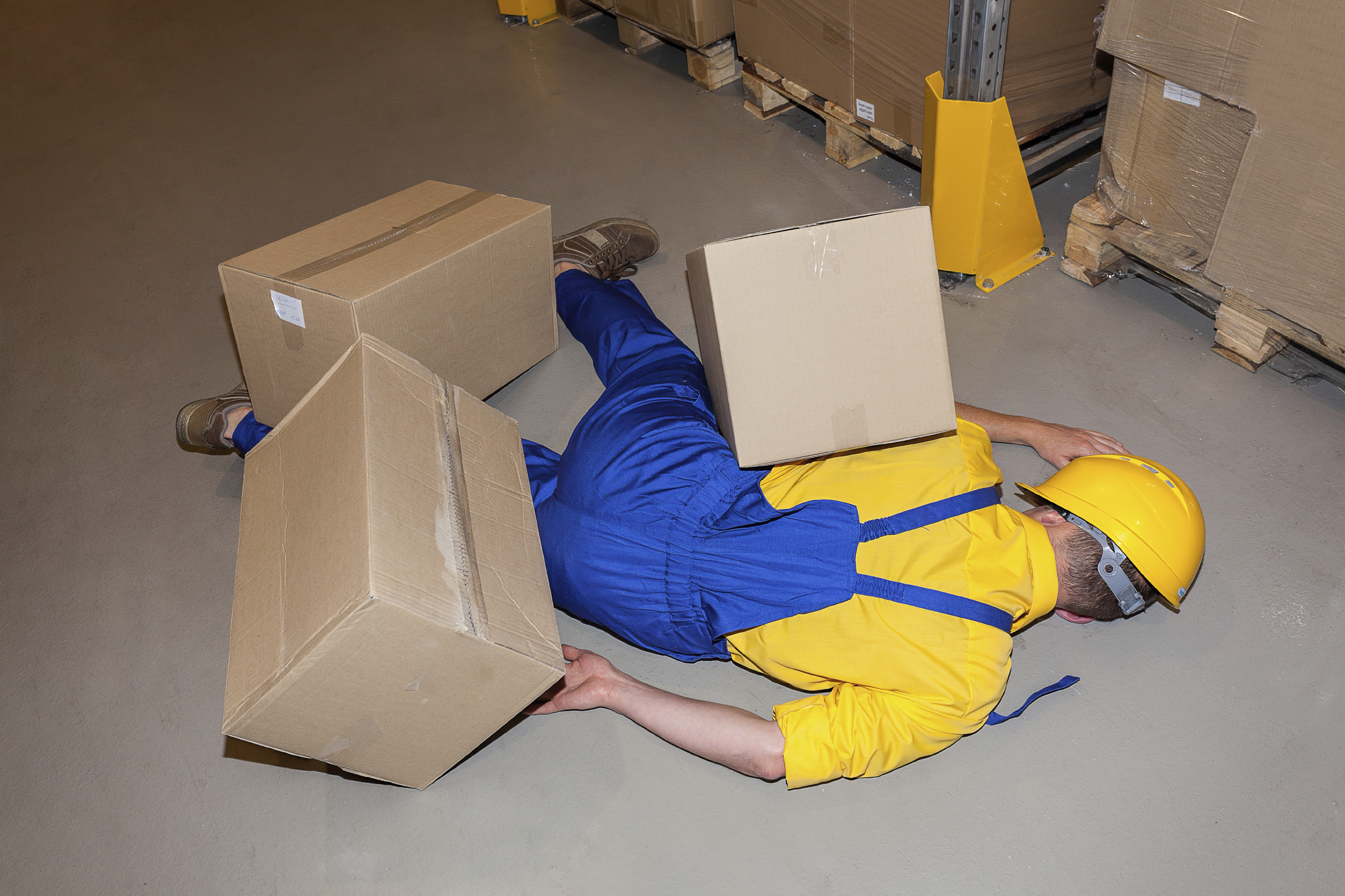
The Health and Safety Executive (HSE) advises employers to follow five steps when carrying out a workplace risk assessment.
Step 1
IDENTIFY THE HAZARDS
ie, anything that may cause harm, such as chemicals, electricity, working from ladders, goods piled high in the stockroom.
A good starting point is to walk around your workplace and consider any activities, processes or substances used that could injure or cause ill-health to your employees.
We have put together a prompt list of the types of possible hazards you might spot in your business.
Offices – Computer wires trailing across the floor, a loose carpet tile or an overloaded plug socket.
Shops – Promotional displays obstructing parts of the shop, or goods piled high in the stockroom.
Care homes and hospitals – Upper limb disorders associated with repetition of handling and moving vulnerable people; inadequate guard or hand rails on stairs; violence to staff (frontline patient services).
Garages – Burns from battery acid, car fumes causing breathing problems, a car jack failing.
Factories – Faulty equipment, slippery factory floor, flammable liquids.
Hair dressing / beauty salons – Substances that may damage the eye, or that may cause harm by coming into contact with the skin, or by being swallowed.
Building sites – Exposed cables, vehicles exiting site vehicles on site, injuries resulting from repetition of manual handling of tools, operating machinery, working at heights; fall of workers, tools, materials etc, inaccurately erected scaffolding. Falls from height are one of the biggest causes of workplace fatalities. LINK
Farms – Machinery with unguarded moving parts, working at height (ladders, rooftops, silos), chainsaws.
Pubs / restaurants / hotels – Hot surfaces (burns and scalds), cutting equipment, spillages causing slippery floors, old pipes and beer lines, musculoskeletal (eg back, knee pain) disorders from repetitive work making beds or carrying luggage, hazardous chemicals (cleaning agents).
Step 2
DECIDE WHO MIGHT BE HARMED AND HOW
Who’s at risk apart from your employees? Are there contractors or visitors or members of the public who might be harmed?
You could involve your employees in the process by consulting them about what they think the hazards are - they may notice things that you have missed and have some good ideas on how to control the risks.
Identifying groups of people (eg people working in the stockroom, lone workers) who might be harmed will help you identify the best ways to control the risk.
Step 3
EVALUATE THE RISKS – ASSESS THE RISKS AND TAKE ACTION
After identifying the hazards, you then need to decide how likely it is that harm will occur ie the level of risk and what to do about it.
The risks need to be prioritised ie ranked in order of seriousness, and the risks need to be made small by either eliminating / eradicating the hazard therefore preventing the hazard eg erecting a machine guard, or adding a non-slip surface; or brought under control, so that harm is unlikely.
The Management of Health and Safety at Work Regulations 1999 set out safety management guidance for employers for tackling risks.
You may have heard of adapt the work to the worker - a basic principle of the legislation. For example, in an office chairs and display screen equipment (DSE) are adjustable to the individual.
It is also recommended that employers “provide training in safe working systems.”
Personal protective equipment (PPE) is routinely adopted in some industries to all staff at risk, with the appropriate training in when and how to use this equipment, such as appropriate eye protection, gloves, special clothing, footwear.
Hard hats are widespread in today’s workplace; they were invented to protect workers from falling objects and from bumping their heads and from electrical exposure. Hard hats are a crucial feature of worksite safety to protect workers in environments that can prove unexpectedly hazardous; they are a proven means of saving lives in the workplace.
Step 4
MAKE A RECORD OF THE FINDINGS
Employers with five or more staff are required to make a written record of the main findings of the risk assessment. The findings you should write down include who could be harmed by the hazards and how; the hazards have been recognised and highlighted; reasonable precautions (protocols) have been put into place. These can be compared with the good practice guidance on the HSE website.
The risk assessment is a working document; you should be able to read it, it shouldn’t be locked away in a filing cabinet. It’s good practice to discuss the findings with your employees / staff and display the document for everyone to see.
Step 5
REVIEW THE RISK ASSESSMENT
Think of a risk assessment as a starting point for developing necessary processes to support risk management, health, safety and accident prevention.
It should be seen as a continuing process; as such it is subject to continual review and revised if and when necessary.
Any actions identified as being necessary to control risks can be ticked off once implemented.
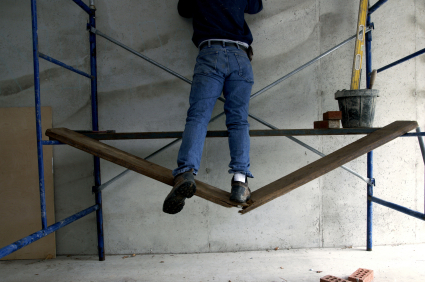
What is a risk assessment?
Regulation 3(1) of the ‘Management of Health and Safety at Work Regulations 1992 states:-
•‘Every Employer shall make a suitable and efficient assessment of:-
a) The risks to the health and safety of his employees to which they are exposed whilst they are at work.
b) The risks to the health and safety of persons not in his employment arising out of or in connection with the conduct by him or his undertaking;
•For the purpose of identifying the measures he needs to take to comply with the requirements and prohibitions imposed on him by or under the relevant statutory provisions.’
What is a hazard?
Hazard :
The potential to cause harm. Harm including ill health and injury, damage to property, plant, products or the environment, production losses or increased liabilities.